Process Simulation
- António Sousa
- Sep 16, 2022
- 5 min read
Updated: Nov 28, 2023
INTRODUCTION
Over time, the approach to process development, as well as the expectations regarding its results, have evolved. Initially, the focus was on the ability to solve problems quickly, almost immediately after the start-up of the process. These corrective actions, for those familiar with the Lean Production System definitions, can be considered waste.
More experienced organizations quickly recognized the need to avoid production problems in the process design phase, and several approaches thus emerged, such as Design for Manufacturing, Design for Six Sigma, 3P (Production Preparation Process).
These approaches help to identify and prevent many problems, resulting in a complete and well-designed process. The definition of the solution considers the voice of customer (VOC), voice of business (VOB), prioritization of requirements, risk assessment and possible mitigation strategies. The result is a shorter ramp-up, lower product cost, and adequate process capability.
Despite all the evidence provided by these methodologies, we can't help but wonder about the unexplored potential. What would happen if we could experiment more, without material costs or development time? How could we better prepare the process if we exposed it to the variations observed every day, in real life?
PROCESS SIMULATION
The concept of process simulation introduces a component of experimentation in the design phase of the process, which allows its optimization, without negative impact in terms of operations disruptions (test runs on existing processes) and in terms of material usage or equipment and employees occupation.

Experimentation aims to answer the following challenges and questions in the design phase of a process:
Is it necessary to invest in a new machine?
Can the current process meet the expectations?
How will the delivery time change due to changes in work shifts?
What is the best strategy for resource allocation?
What is the true impact of quality improvement on the delivery time?
What is the impact of variation on results?
How do we respond to the challenges of an operational context that is changing more and more frequently?
To carry out simulations models are needed. Models are approximations, to a greater or lesser degree, to reality.
We can identify different types of models in the following chart, with examples of each category:

We can describe static models in a simplified way as:
Models that do not "execute" a task or an algorithm
Models in which all experimentation and analysis is performed by the users
Models have long been used in many continuous improvement activities.
The maps resulting from a VSM (Value Stream Mapping) analysis are perhaps the best-known application of static models.

Dynamic models:
"Execute" a task or an algorithm
Allow much more timely experimentation and are better suited to complex problems
Require computational power
Dynamic models can be splited into 2 categories:
Deterministic dynamic models: they determine the optimal response given a set of restrictions
Stochastic dynamic models: they take into account the process variation and the demand variation. They are not built to give only one optimal answer to a given problem
There are many solutions in terms of simulation applications/software, such as Flexsim, Anylogic, Extendsim, Arena, Process Playground, among many others. The solutions in the market have functionalities oriented to the organization of the process (scenarios, parameters, sequence of operations, distribution of operators), as well as others directed to the physical simulation of workstations. Not all solutions have these two types of functions, but others cover all these aspects and have 3D process design and animation. So, the software selection must be careful and consider the simulation needs as well as its complexity.
The simulation of processes through stochastic dynamic models has many advantages:
Allows exploring possibilities - testing the impact of process variants, procedures, or resource allocation without disrupting normal operations
Evaluation of the impact of diferent sets of process parameters
Exposes the modelled process to variation in demand, variation in equipment efficiency, variation in resources
Allows a more correct assessment of the robustness of the process, in a realistic scenario
Helps to validate the results and to anticipate risks
On the other hand, we can also identify some difficulties and obstacles to the implementation of this type of analysis:
Complexity: it may be difficult to model all the functionalities of the system/it may be necessary to split the system into more than one model
Requires time and resources - the software is not always known and used frequently, which requires training or finding trained people. It is also essential to know the reality, which requires involvement in the process
The problem may be easier to analyze and solve with an analytical method
Direct experimentation on the real system may be faster, more economical, and have lower risk
APPLICATIONS OF PROCESS SIMULATION
Process simulation can be applied with advantages in many industry scenarios such as:
Production and Assembly
Determine the number of employees, machines and cells required
Evaluate different production planning alternatives
Determine the production capacity
Determine the number of containers needed
Study alternative line configurations
Set batch size
Production sequencing
WIP location and calculations
Line balancing
Planning of shift and breaks
Material Handling
Determine the frequency of internal logistics systems as well as its capacity
Determining the speed of the conveyor belt
Determining the number of employees in material reception
Logistics and Transportation
Route planning
Dimensioning the number of docks
Evaluation of alternative stock management policies
Study the impact of changing a "hub" in the network
Analysis of different queue management policies
APPLICATION EXAMPLE
Consider an industrial process organized in Pull, like the one represented in the image:
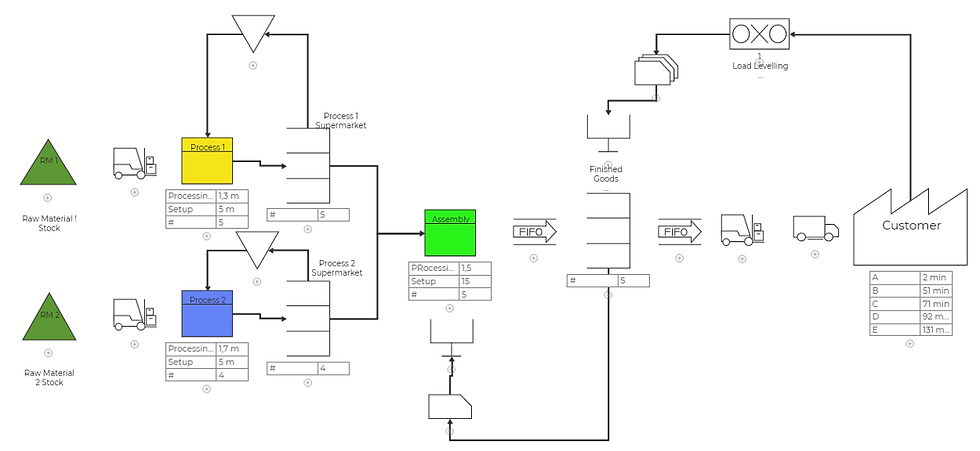
When "running" the simulation and analyzing the data, ww conclude that:
Demand has been fully satisfied
The supermarket (normalized stock) of finished product fulfils its function
When observing the stock levels, the question arises: can we adjust the replenishment levels to lower the average stock and maintain the service level?

Once we change the process parameters and run another simulation, we find that yes, we can:

What if we want to know how this same process will behave when exposed to demand variation, process cycle time variation, or even process setup time variation?
To build this scenario we need to change the parameters and, instead of fixed values, consider a statistical distribution for each of them. Thus, it will be necessary to change the model from the deterministic mode to the stochastic mode. After running the simulation, it is shown that when subjected to variation, the process does not behave as desired, so we need to correct the parameters and run a new simulation:

Da mesma forma se poderia avaliar o impacto da redução do tempo de setup dos equipamentos nos stocks e no leadtime do processo.
Demos assim um exemplo, ainda que descrito de forma sucinta, do que pode ser a experimentação através de um modelo e das suas potencialidades.
In the same way one could check the impact of reduced setup times on stocks and process lead time.
This a brief example of what can be achieved by experimenting with a simulation model.
SUMMARY
The evolution of digital simulation tools has been booting its adoption. The increase in computational power allows the use of more complex models, as well as "running" the simulation more often and having data closer to reality. The very concept of the digital twin present in the 4.0 approach breathes new life into simulation models. Still, the effort can be significant, both in the preparation of the model and in its analysis, so the decision for these tools should be well aligned with the objectives and the level to be achieved in the design of new processes or in the improvement of existing processes.
Simulations performed with Process Playground, by MoreSteam

Comentarios